Producing a Comic Book or Graphic Novel is a big undertaking. You have to develop the story, create the illustrations, design the cover, and determine the physical layout of the book. Before getting too deep into the project it also helps to consider the printing phase of your book. After all, the last thing you need is to be blindsided by an unforeseen surprise when you are ready to print.
Below is a list of six things that will have an effect on the appearance and cost of your comic book project
Binding Style
Because the page count is relatively low, Comic Books are traditionally produced using the Saddle-Stitch binding method. Saddle-stitched books are constructed from folded sheets which are held together by wire staples. The staples are driven through the crease of the book's spine to secure the pages into book form. Though simple, the result is a very professional looking document.
In addition to being the most economical binding style, saddle-stitching allows the book to lie almost flat when opened. This works well for artwork that spans two adjacent pages (crossover images).
Being more of a book than a simple booklet, Graphic Novels generally have a higher page count than Comic Books. Graphic Novels are commonly produced using the Perfect Binding method to accommodate this higher page count.
Perfect bound books are created by gluing the pages and cover together at the spine with a strong, flexible glue. The other three sides of the book are then trimmed as needed to give them clean "perfect" edges. Unlike the saddle-stitch method, perfect binding often allows for printing on the book's spine.
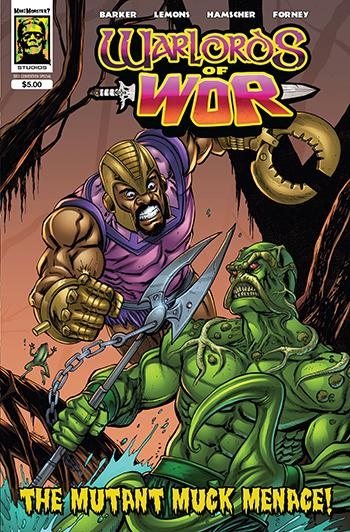
Standard Comic Book Size
The standard size for a Comic Book is 6-5/8 inches wide by 10-1/4 inches high, though no rule that says you can't vary from this somewhat.
Graphic novels have no standard size and can be printed in just about any dimension you desire. That said, your printer may make size suggestions to help keep your production and distribution costs as low as possible. A few subtle design changes upfront could translate to big savings later.
Quantity
The quantity of books will determine the type of printing press best suited for producing it. For example, if you only need 200 or 300 copies of your book, you will generally achieve a lower unit cost by printing your books with a digital printing press. This is because a digital printing press has minimal set-up costs associated with a production run. An offset press, on the other hand, has higher set-up costs which cannot be efficiently distributed across a small production run.
However, as the order quantity increases, to say 500 or 1,000 books, offset printing becomes the more economical production method. Even though the set-up cost of offset printing is higher, a larger order allows this cost to be distributed across more books. And once an offset press is running, the actual cost of applying ink to paper is substantially less than a digital press.
Incidentally, just because the unit cost of a book decreases as the order quantity increases, it is still wise to consider which run size is optimal for your specific situation. A lower unit cost is great, but not if you're ordering more books than you'll ultimately need.
Page Count
The page count of your comic book or graphic novel (along with the total number of books needed) will help your printer calculate how much paper is needed to produce your project.
By the way, when relaying the page count to your printer, be sure not to confuse sheets with pages. Basically, every sheet within the book represents two pages. Even if a sheet in the book is blank on one side, or is blank on both sides, your printer will count it as two pages. Thus, there will always be twice as many pages as there are sheets within a book. 100 sheets = 200 pages.
Another thing to keep in mind about a saddle-stitched book is the page count must be in multiples of four (4). This is because saddle-stitched books are created from folded sheets.
Ink Colors
Most Comic Books and Graphic Novels are produced with a full-color cover and full-color pages. In some cases, black ink may be the more economical choice, but full-color provides maximum impact and perceived value. Sometimes there can be a mixture of full-color pages and black ink pages.
Also, your printer may ask if the ink coverage extends all the way to the edge of the pages or cover (called a Bleed). Depending on the project, an ink bleed may cost slightly more because it requires printing on a larger sheet of paper and then trimming the paper down to the desired size.
Paper Characteristics
The paper characteristics you select - such as thickness, texture and sheen level - largely depend on the image you are aiming to project. For example, a book made with a heavier, lustrous cover provides a higher image of quality than a thinner, duller cover.
Also, a variety of paper coatings are available to enhance your book's look and durability. For example, you may wish to have a clear coating - such as a gloss UV or laminate - applied to the cover of your Graphic Novel. Gloss UV and lamination not only increase the durability, these coatings also enhance the vibrancy of the ink colors.
To save money, the cover of a saddle-stitched Comic Book can be the same thickness as the interior pages. This is referred to as a "self-cover."
If you have any questions about an upcoming Comic Book or softcover Graphic Novel project just give Formax a call at 866-367-6221. Or, if you already know your specifications and would like to receive a quote, submit our quote request form. We look forward to assisting you!
Take Care,
Rick